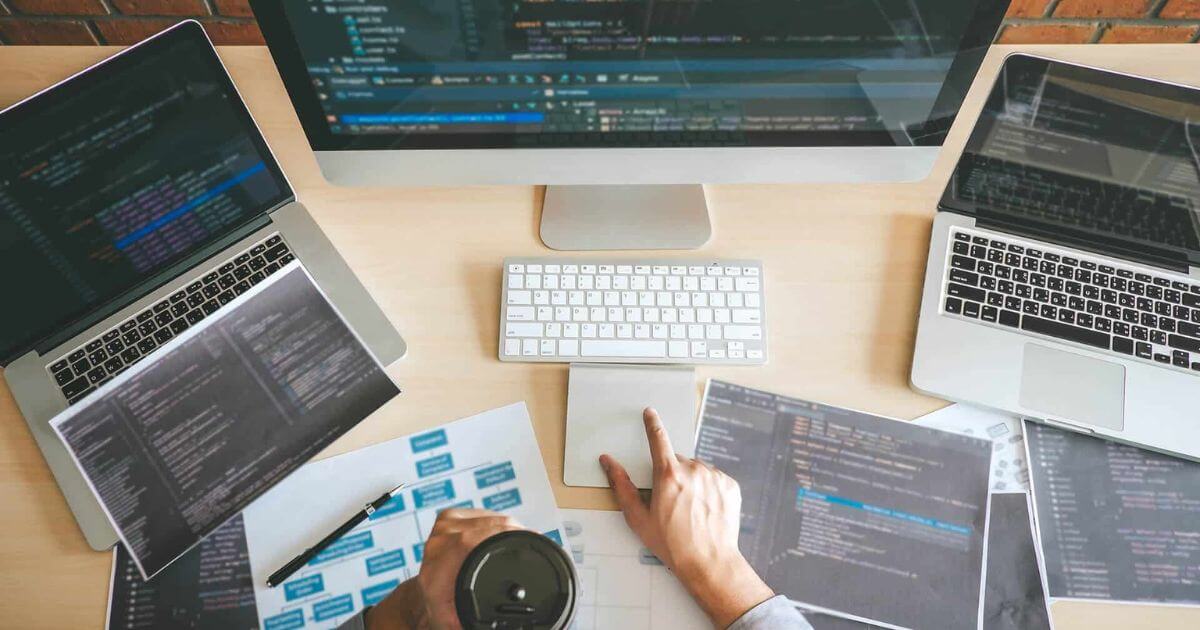
Pressure Converter
Pressure Converter
Imagine a ship battling turbulent seas; its ability to navigate depends on precise adjustments to the sails. Similarly, a pressure converter plays a vital role in managing the pressures of fluid or gas in industrial applications. By maintaining ideal pressure levels, these devices not only enhance efficiency but also protect valuable equipment. But what happens when these converters malfunction, or how do you choose the right one for your needs? Understanding these aspects could be the key to ensuring smooth operations in your processes.
What Is a Pressure Converter?
A pressure converter is a device that changes the pressure of a fluid or gas from one level to another, making it an indispensable tool in various industrial applications. You might find these devices in sectors like manufacturing, oil and gas, or HVAC systems. They help guarantee that processes run smoothly by maintaining ideal pressure levels necessary for equipment operation.
These converters come in different forms, such as pneumatic and hydraulic types, depending on whether they handle gases or liquids. If you're working with hydraulic systems, for example, you'll often need a hydraulic pressure converter to maintain the high pressure required for lifting or moving heavy objects.
On the other hand, if you're dealing with pneumatic systems, then a pneumatic pressure converter will be vital for regulating airflow and providing precise control.
When you're selecting a pressure converter for your application, you'll want to take into account factors like pressure range, flow rate, and efficiency. These characteristics will directly impact how well it meets your operational needs.
Ultimately, understanding the role of pressure converters can greatly improve your systems' effectiveness and reliability in any industrial setting.
How Pressure Converters Work
How do pressure converters adjust fluid or gas pressure with such precision? The answer lies in their engineered mechanisms that respond to varying flow conditions. When you apply a differential pressure across the converter, it activates a sensor that detects these changes. This sensor is essential: as pressure fluctuates, it relays signals to the control system, guaranteeing real-time responses.
Inside the converter, a diaphragm or piston works to either open or close a valve. This action modifies the flow area, allowing you to maintain the desired pressure.
It's all about balance — by continuously monitoring the output, the converter can make minute adjustments that assure your system operates smoothly.
Moreover, many pressure converters come equipped with feedback loops. These loops provide constant data, allowing you to refine adjustments even further. With these components working together, the converter effectively manages pressure across various applications while minimizing fluctuations.
In essence, a pressure converter's design allows you to achieve specific pressure settings efficiently and accurately, making your processes more reliable and effective. Understanding this mechanism empowers you to optimize your systems wherever precise pressure control is crucial.
Types of Pressure Converters
When considering the various types of pressure converters available, it's vital to recognize that each type serves specific applications and functions.
You'll typically encounter three main types: pneumatic, hydraulic, and electronic pressure converters.
Pneumatic pressure converters utilize compressed air to generate pressure changes. You'll find these commonly in industries that rely on air-powered tools or automation systems, as they're efficient and cost-effective for many tasks.
Hydraulic pressure converters, on the other hand, use liquids — often hydraulic fluid — to transfer pressure. This type is widely utilized in heavy machinery and equipment, where high force is indispensable.
Hydraulic systems are known for their power and precision, making them an excellent choice for tasks requiring significant lifting or movement.
Lastly, electronic pressure converters use sensors and electronic components to convert pressure readings into readable data. You might opt for these in more specialized applications where precision and real-time monitoring are required, such as in research facilities or sophisticated manufacturing processes.
Each type of pressure converter has its unique advantages, so it's important to assess your specific needs to choose the right one for your application.
Common Applications
Pressure converters find diverse applications across various industries, and understanding these can help you identify where they might benefit your operations.
In the manufacturing sector, for example, you often use pressure converters to regulate and control the pressure in hydraulic systems, ensuring ideal performance and safety during production.
In the automotive industry, pressure converters play a vital role in fuel and brake systems, allowing you to maintain precise pressure for efficient vehicle operation.
Similarly, in the aerospace sector, these devices help manage cabin pressure and keep systems running smoothly.
If you're involved in water treatment, pressure converters help you measure and adjust pressures in filtration systems, ensuring effective purification processes.
In HVAC systems, they're essential for modulating air pressure, helping you maintain comfortable indoor environments.
In the oil and gas industry, you utilize pressure converters for monitoring and controlling pipeline pressures, enhancing safety and efficiency in operations.
Regardless of your field, incorporating pressure converters can streamline your processes and improve system reliability.
Understanding these applications enables you to identify opportunities for increased performance and efficiency in your work environment.
Benefits of Using Pressure Converters
In recent years, the advantages of using pressure converters have become increasingly evident across various industries. One of the primary benefits is their ability to improve efficiency. By transforming pressure into a usable form, these devices help you streamline operations, reducing energy consumption and lowering costs.
Furthermore, as highlighted in the Industry Application section, pressure converters are essential tools in managing hydraulic and pneumatic systems, further showcasing their critical role in engineering.
Another advantage is enhanced precision. Pressure converters provide accurate control of pressure levels, ensuring that processes run smoothly and safely. You'll notice fewer errors and reduced waste, which translates into better product quality and customer satisfaction.
Additionally, pressure converters are versatile. They can handle a range of applications, from manufacturing to telecommunications, making them a valuable asset in different settings. Their adaptability means you can integrate them into existing systems with ease, improving overall performance.
Maintenance is also simplified with pressure converters. Their robust design often results in fewer breakdowns and a longer lifespan, giving you peace of mind and minimizing downtime.
Selecting the Right Pressure Converter
Choosing the right pressure converter can greatly impact your system's performance and efficiency. Start by evaluating your specific application and its requirements. Consider factors like pressure range, flow rate, and the type of fluid you'll be converting. Different converters are designed for varied conditions, so knowing your needs helps narrow down the choices.
Next, think about the accuracy and reliability of the converter. You want one that can maintain precise measurements over time, which can prevent costly errors in your processes. Check for industry certifications and reviews to verify you're selecting a reputable product.
Also, consider the installation and operation costs. Some converters may be cheaper upfront but could lead to higher expenses down the line due to maintenance or inefficiency. Look for an option that balances initial investment with durability and long-term savings.
Lastly, don't underestimate the importance of after-sales support. Having reliable customer service and technical assistance can make a huge difference when you're implementing and using your pressure converter.
Maintenance and Troubleshooting
While regular maintenance is essential for guaranteeing your pressure converter operates efficiently, troubleshooting can help you quickly identify and resolve issues as they arise.
Start by inspecting the connections and seals for any signs of leakage. If you notice gas or fluid escaping, tighten or replace those fittings immediately.
Next, check the pressure readings. If they're inconsistent or outside the expected range, recalibrate the device according to the manufacturer's instructions.
Cleaning clogged filters or vents is another key step. Dirty components can restrict flow, impacting performance.
Listen for unusual noises; grinding or hissing sounds often signal underlying issues. Power fluctuations can affect performance too, so monitor your electrical connections for any faults.
Don't forget to review the user manual for specific troubleshooting tips relevant to your model. If you've gone through these steps and the converter still isn't performing, it might be time to contact a professional.
Regular maintenance tasks include checking fluid levels, changing out worn parts, and performing system resets as needed.
Conclusion
In the world of industrial processes, "a stitch in time saves nine," and investing in the right pressure converter now can save you time and money down the line. Whether you're boosting efficiency in manufacturing or ensuring safety in oil and gas operations, these devices are essential. By choosing the right type and prioritizing maintenance, you'll enhance performance and prolong equipment life. So take action today and optimize your operations with a reliable pressure converter!